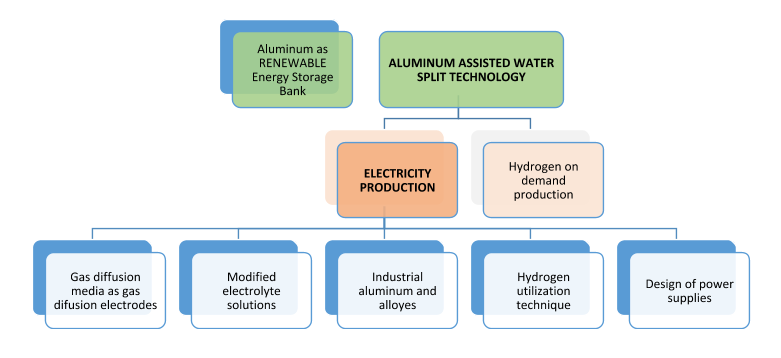
Energy Storage Bank
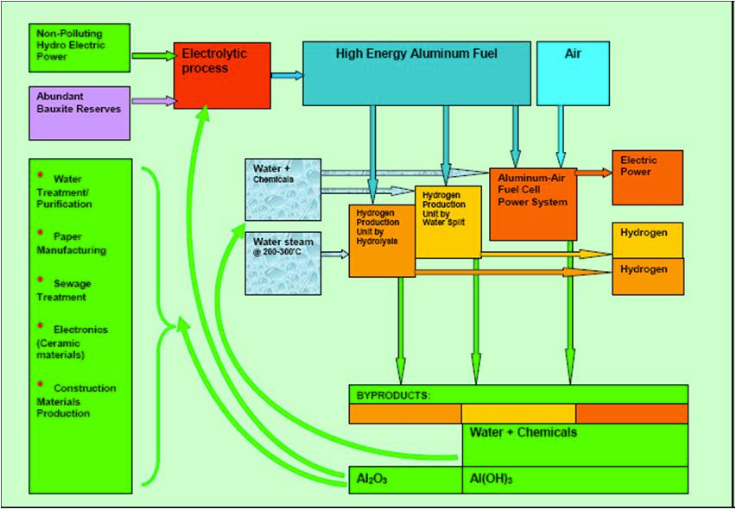
Gas diffusion media as base of Gas Diffusion Electrodes and Membrane Electrode Assemblies for Fuel Cells AFG has developed a commercial manufacturing process that allows for hands-free fabrication of fully reproducible GDEs. The core of this technology is an extruded all-in-one design:
1. Oxygen/air Gas Diffusion Electrodes (GDE) for alkaline metal-air (particularly aluminum-air) fuel cells.
2. Membrane Electrode Assembly (MEA) for PEM Fuel Cells.
AFG’s MEAs, based on its proprietary GDE technology, are suitable for both PEM and Alkaline fuel cells and for portable, residential and transportation applications.
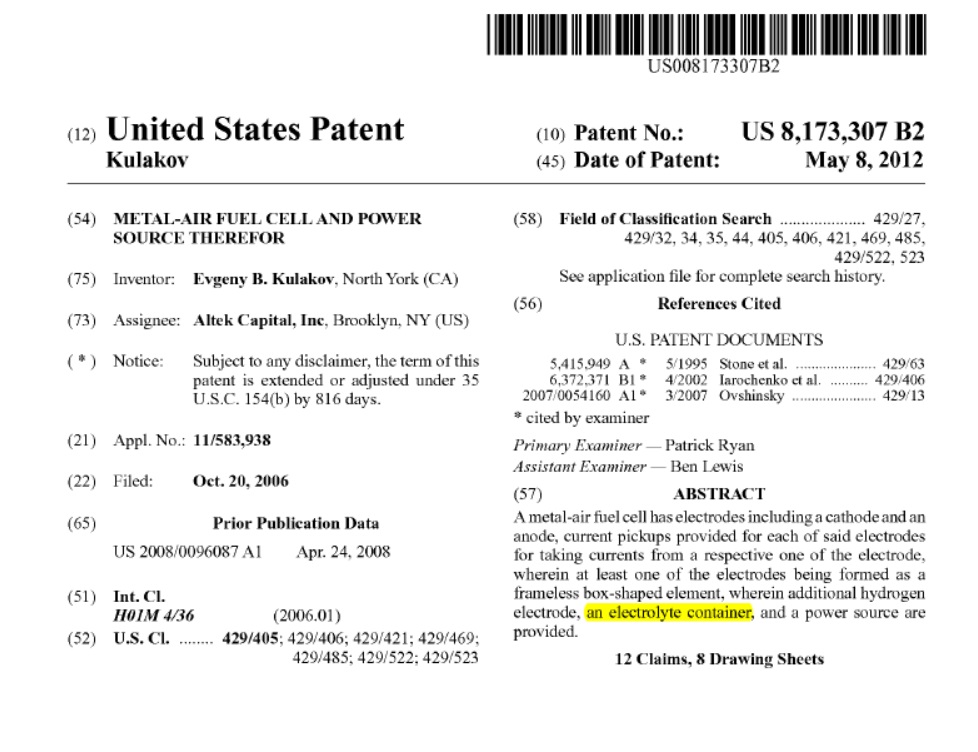
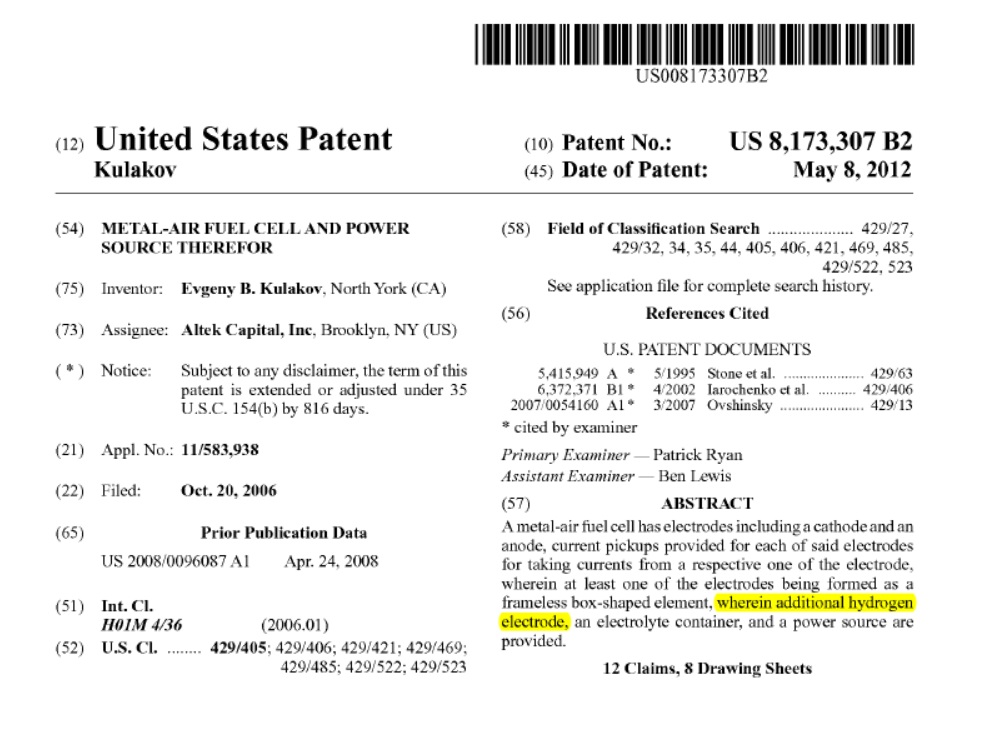
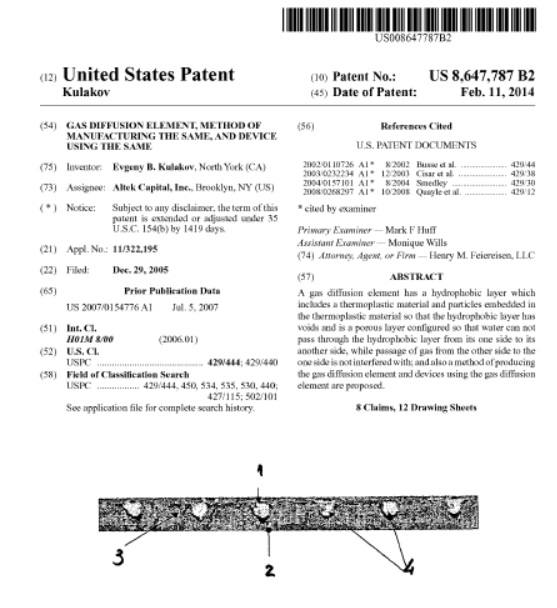
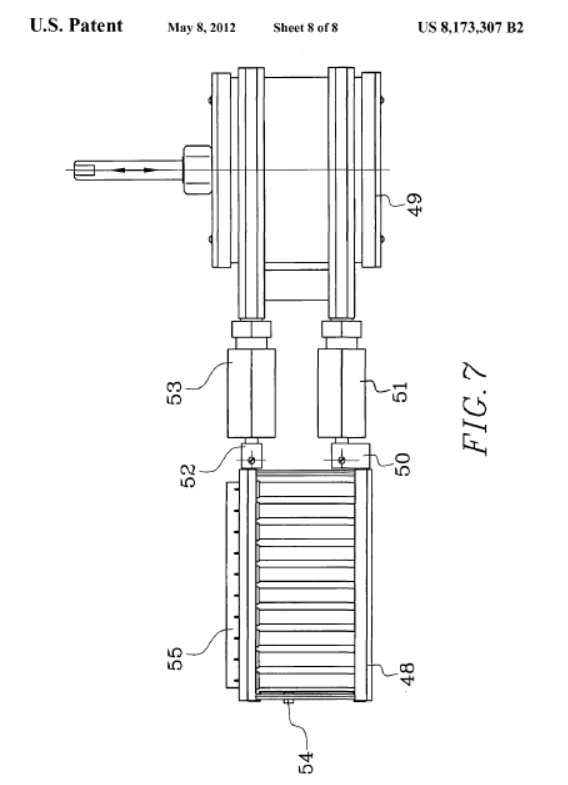
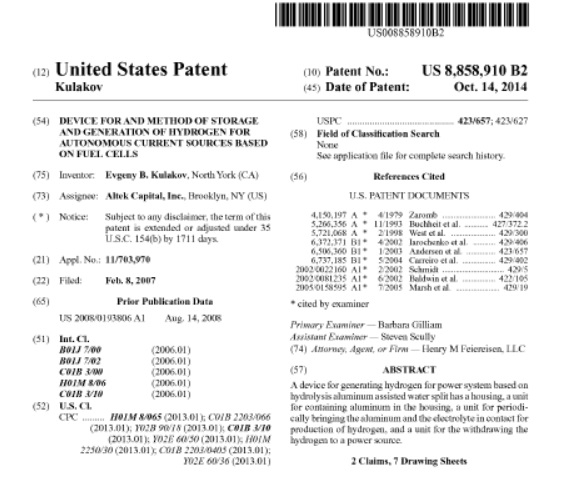
Aluminum has been a most sought after source of energy for more than 50 years, because of its inherent high energy density, its being lightweight and its being recyclable (a more detailed presentation of aluminum is available in Appendix III). Aluminum has already proven itself to be a viable material in battery applications. The Zaromb cell, produced in 1960, stored 15 times the energy of a comparable lead acid battery.[1,2]
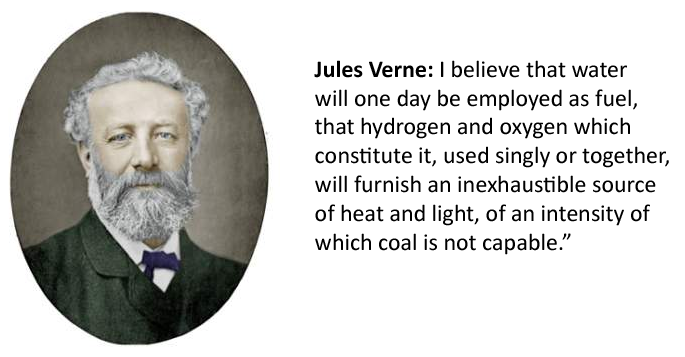
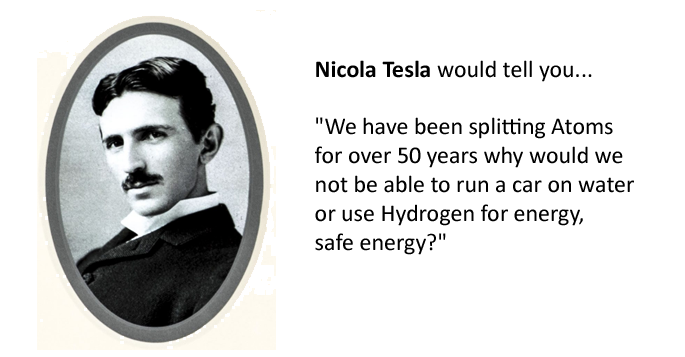
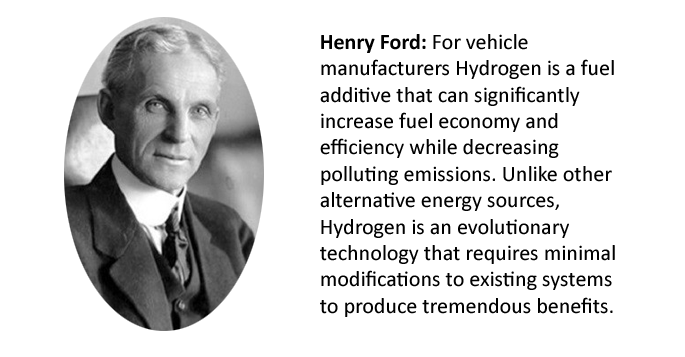
Fuel cells using different metals really began more than 25 years ago. The driving force in these endeavors was the need to find a reliable, lightweight power source for sophisticated, military and space applications. The weight and limited shelf life of traditional batteries was just not acceptable. Initial attempts, unfortunately, had substantial drawbacks due to corrosion.[3,4] Other attempts led to the use of tine, indium, thallium, iridium or gallium to lower the corrosion. Since the year 2000 some companies, particularly Aluminum Power, Inc., as well as Voltek, Inc., and eVionyx, Inc., have attempted to produce small aluminum-air cells for portable applications.[5] The challenge has been to manufacture cost competitive, efficient products. Most companies have used aluminum alloys in production, at a significant cost increase.[6,7] In addition, expensive additives were added to the mix. Both these issues hampered the recycling of the by-products and created unwanted wastes. These factors, combined with the inability to create an affordable final product, substantially reduced the general commercial viability for all but specialized uses.
Undertaking a completely new approach to the use of aluminum as the source of energy for fuel cells included the use of industrial aluminum and a more optimized electrolyte mixture to dramatically release the inherent energy. Because there were no alloys to separate it from, the resulting mix could easily be recycled (see an aluminum recyclable life cycle in Appendix I). Furthermore, the use of proprietary, but readily available, chemical formulations will simplify the process to a viable commercialized product.
At the present time there are two substantial technologies that utilize the use of aluminum as the key ingredient. One is known as the Alkaline Aluminum-Air Fuel Cell Technology and the other is the Hydrogen Production for Fuel Cell Technology. br> While most other hydrogen-based fuel cell technologies rely on hydrogen stored in a pressurized gas or liquid form, these new technologies derive their power from water and a solid–state fuel. More energy can be liberated over a much longer period of time at a significantly reduced cost, because of the higher relative density of its power source. It is anticipated that aluminum-air fuel cells will be substantially simpler and lower in cost than others, such as PEMFC, Lithium Ion or Nickel-Metalhydride batteries.
Integrated into both these technologies are the crucial uses of both the on-board and the on- demand production of all the required energy. All the energy is held within the aluminum and water until it is requested. There are no outside storage units, nor any problem with stability or combustion.
- Al-Air Fuel Cell The aluminum-air fuel cell is composed of an aluminum anode set in an aqueous alkaline solution and utilizes a gas diffusion electrode/cathode. The emission-free oxidation of aluminum by oxygen from ambient air provides an efficient power supply. The safe and efficient proprietary components can be housed in a fully self-contained unit. One key to this technology is the use of two quickly replaceable cartridges, one containing the aluminum anode and the other containing an electrolyte mix with water. Once the anode cartridge is replaced, it can be recycled back to aluminum dozens of times for many years (a more detailed presentation of an alkaline fuel cell is available in Appendix II)
- Hydrogen for Fuel Cell The hydrogen production system is a fully self-contained unit that is capable of producing a virtually unlimited environmentally safe source of hydrogen and it requires no high-pressure storage tanks. This creates unique advantages for utilizing this system, including military applications or for any hydrogen production and storage requirements (perhaps for extensive transportation “refueling” stations). On a technical note, it uses fully recyclable, relatively low cost and easily available chemical components and displays a highly efficient hydrogen output. The high performance, moderate cost, and the level of enhancements in the availability of an ongoing source of pure hydrogen without any pressurized containment, makes this system unlike any other on the market today.
The chemistry components for the two methodologies have some similarities, including some of the basic ingredients and residuals. However, the concepts have some differences and are shown below (a more detailed scientific analysis is available in Appendix IV).
- Alkaline – Aluminum-Air Fuel Cell Technology This technology generates electricity by converting the internal (heat and chemical) energy of aluminum, water and the oxygen supplied from the surrounding (ambient) air directly to electrical power (with no combustion or moving parts) through a controlled chemical reaction. The generated power is therefore inherently ultra clean, highly efficient and reliable.
- Hydrogen Production for Fuel Cells and Other Applications The contemporary technologies for hydrogen production for fuel cells use two different methods, depending on the particular application required. Both methods are based on hydrogen production from a water source and assisted by aluminum as an active catalyst.
Having reviewed the history of aluminum energy for fuel cells and its present capabilities, one must conclude that the utilization of aluminum for fuel cells should become an integral part of the solution for an economically, clean, non-polluting source of energy. Its ability to be used in a wide range of applications lends itself to the possibility that one or more of its inherent characteristics will be a most efficient choice for any number of critical uses. Given its abundance, lightweight and its being fully recyclable, the opportunities for the commercialization of the multiple technologies are quite evident. Certainly numerous design and manufacturing issues still exist, but because the critical technological challenges have been resolved, the potential is certainly quite high.